The Suez Canal and Panama Canal connect critical international trade and supply chains across continents. The Suez Canal (completed in 1869) routes ships between Europe and Asia directly linking the Red Sea and the Mediterranean Sea. The Panama Canal (completed in 1914) connects ships traveling between the Pacific and Atlantic oceans, reducing shipping around South America by 15,000 km. Given that between 80–90% of the world’s goods are transported by sea, global supply chains rely heavily on these two maritime “shortcuts.” .
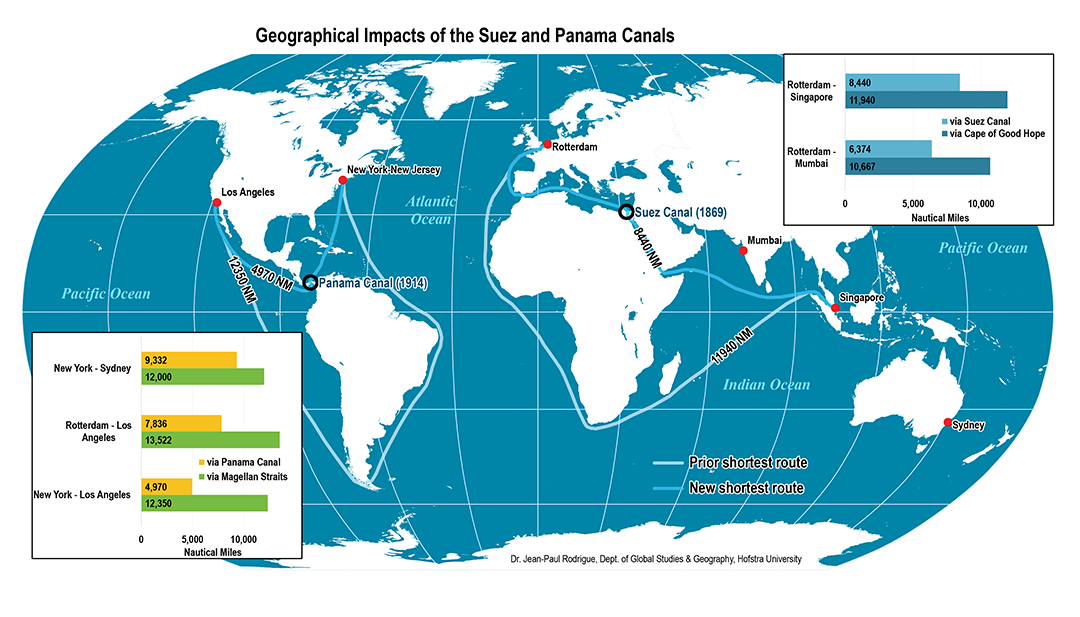
The Geography of Transportation System’s Geographical Impacts of the Suez and Panama Canals
Freight volumes passing through each of these important shipping passageways decreased dramatically in recent months on account of distinct emergencies in the area affecting safe and orderly passage. The ultimate duration of these interruptions is unknown. However, the impact on trade in January 2024 is clear. Companies in the U.S. and around the globe will likely feel ripple effects, if not more serious interruptions to supply chains in the coming months. This comes at a time when global supply chains are already reeling from the increasing freight costs, delivery delays, and inflation that mounted over the last three years. To anticipate, prevent, and address additional challenges and fallout, manufacturing companies should consider the steps outlined below to reduce their risk related to transportation costs and delays.
Recent Problems Impacting Global Trade
Governments, commercial businesses, and economic experts are monitoring at least two major crises in the global supply chain. First, since December 2023, commercial vessels traversing the Red Sea to reach the Suez Canal—a crucial trade route between Europe and Asia—began suffering from sustained attacks by Houthi rebels in Yemen. The rebels claim the attacks respond to the ongoing war between Israel and Hamas in Gaza and that ships targeted are connected to Israel. Many of the vessels hit, however, have had little to no apparent link to Israel.
Nearly 15% of global shipping traffic is estimated to pass through the Suez Canal in a given year. The volume of freight traversing the Suez Canal decreased dramatically since December 2023 due to the Houthi militant attacks. According to the United Nations Conference on Trade and Development, the number of ships transiting the Suez Canal dropped by 39% since December, resulting in a 45% decrease in freight tonnage. For example, on January 2, 2024, a large Danish shipping company, Maersk, ceased all operations in the Red Sea until further notice after one of its vessels was attacked. Maersk now routes its cargo ships around the Cape of Good Hope—an alternative path that adds weeks and thousands of dollars of expense to each journey. Other companies still braving the Red Sea face skyrocketing costs for shipment containers. To illustrate, in December 2023, the price per container was approximately $1,400. By January 18, 2024, the price for the same container was nearly $3,800—a more than 150% increase.
The Panama Canal—which ordinarily carries approximately 40% of all U.S. container traffic—is simultaneously experiencing interruption due to an unprecedented drought. Drought conditions have decreased water levels of the canal to well below normal levels and forced canal authorities to decrease the amount of traffic navigating the canal each day by more than 36%. This reduction increases shipping delays, which in turn, increase freight costs. And, as with the reroutes from the Red Sea to the Cape of Good Hope, the use of alternate routes exacerbates these delays and costs.
How long each crisis will last is uncertain. The interruptions at the Panama Canal are likely to improve as soon as the region receives rainfall. The current conditions may persist for the near term because the Panama dry season is just beginning and rainy season does not begin until May. The situation in the Red Sea is even less certain. Though, many world governments, including the United States, are supplying various forms of military support to deter the rebels and decrease further attacks in the area.
While little can be done to control these urgent situations, manufacturers can take steps to reduce their risk from unexpected transportation costs and delays. These steps may not prevent unexpected supply chain challenges from arising, but preparing for the unexpected can reduce its adverse impacts.
Reducing Risk Related to Transportation Costs and Delays
As we have previously written about on this blog, several approaches exist to reduce risk related to transportation delays and increased freight costs. Companies may: (1) assess options for a consistent supply by dual sourcing goods using geo-diverse suppliers; (2) consider moving production locations to reduce the distance the product must travel; and (3) evaluate insurance policies and commercial contracts to better allocate delivery delay.
Dual Sourcing
Dual sourcing (i.e., using one or more suppliers to source a material) may yield a more stable supply of materials for their products. Ideally, the key suppliers are located in diverse geographic locations so that a weather issue or other local interruption does jeopardize the entire supply chain. Dual sourcing presumes alternative suppliers exist, which is not always the case. Assuming they do, a company must evaluate the cost of alternative suppliers in comparison to the impact of delivery delay and freight costs in a global supply chain disruption. Assessing the alternative sourcing options and doing the work to identify and qualify additional suppliers is good preparation for the inevitability of supply disruptions.
Onshoring and Nearshoring
Onshoring means moving overseas production to the domestic company’s location. Nearshoring refers to moving overseas production nearby the domestic company’s location, usually in a neighboring country on the same continent. Moving some or all production closer to consumer markets almost always results in reduced transportation costs, though those reductions must be balanced against the cost to move production and related costs, such as the cost of labor. Often companies find that the reliability that comes with onshoring or nearshoring outweighs any associated cost increase. For more information and analysis on this consideration, see Accelerating Trends: Assessing the Supply Chain in a Post-Pandemic World.
Insurance Coverage
Companies should consider insurance to transfer risk for goods lost or delayed in transit. For each day the Ever Given, a quarter-mile-long ship, became lodged in the Suez Canal in March 2021, the blockage prevented cargo worth $10 billion from moving through the canal.1 Companies with adequate insurance found recourse for their losses by making claims.
Many insurance products offer protection against disruption, like the drought at the Suez Canal. These include cargo insurance, contingent business interruption (CBI) insurance, and supply chain risk insurance. Cargo insurance generally protects shipments of goods from losses, damages, or theft sustained during transit. CBI insurance generally protects against lost profits and extra expenses incurred as the result of an interruption of business suffered by a customer or supplier. Supply chain insurance also typically protects against financial losses arising from your supply chain and covers a broader swath of events than CBI insurance. Some negative events that supply chain insurance could cover include government-related disruptions, pandemics, labor issues, and financial problems.
Commercial Contract Review
Whenever there is a significant change in tide that affects business, companies should consider whether their contracts should be adjusted to further hedge against risk or to take advantage of the current business climate. Some points of analysis with respect to addressing delivery delays and freight costs include:
- Shipping Terms. Regardless of whether a company is on the buy-side or on the sell-side, it should evaluate whether the Incoterms provisions or related shipping terms in its contracts are up-to-date. Common updates include ensuring the Incoterms referenced (a) are the most recent version (Incoterms 2020), and (b) reflect the business’ current practice for delivery. If the current business climate supports a shift, companies may evaluate whether the Incoterms provisions could be updated to further minimize risk of incurring unforeseen transportation costs. In an ideal world for buyers, buy-side Incoterms would be Delivery Duty Paid (DDP) at the buyer’s destination, meaning that the seller is required to pay all import duties, taxes, execute customs formalities, and pay for all transportation costs.2 In an ideal world for sellers, sell-side Incoterms would be Ex Works (EXW) at the seller’s dock, which places the least burden on the seller, only requiring that the seller make the goods available and suitably packaged at the specified point of delivery.3
- Shipment Costs. Every contract for the purchase and sale of goods should explicitly define each party’s responsibility for packaging and shipping costs. Buy-side companies typically prefer transportation costs to be included in the price of the good or fixed. Sell-side companies usually elect to pass transportation costs to the buyer, or for pricing to adjust if transportation costs increase.
- Delivery Delay. Contracts should include detailed delivery terms and companies should ensure their agreements accurately reflect their expectations. Consider:
- Are delivery dates approximate (as is typically desired by the seller)? Or is time of the essence as to delivery (as is typically desired by the buyer)?
- Who will be responsible for arranging and paying for expedited freight in the event of a delivery delay?
- What remedies are available to the buyer in the event of a delivery delay? Are these remedies exclusive (as is typically desired by the seller) or cumulative (as is typically desired by the buyer)?
- Will liquidated damages be imposed if a delivery is delayed (as is sometimes desired by the buyer)? If so, is the liquidated damage provision enforceable in the governing jurisdiction or might it be deemed an unenforceable penalty?
- Would it be more beneficial to have liquidated damages or contract damages? Although a liquidated damages clause helps provide clarity to the parties on damages, it also acts as a cap on damages.
- How do limitation of liability provisions affect the recovery of damages in the event of a delivery delay?
- Force Majeure. Companies should review their force majeure provisions and ensure that the terms address transportation delays caused by continued supply disruptions. Some questions to consider when evaluating force majeure provisions include:
- Do transportation delays, inability to obtain goods or materials, and supply chain constitue “force majeure events”?
- Is there catch-all phrasing that would cover transportation delays, inability to obtain goods or materials, and supply chain issues?
- In the event of a force majeure event, does the buyer have the right to suspend or terminate any purchase orders, and/or terminate the entire agreement under the force majeure clause? Is there a time period after the seller declares force majeure that the buyer must wait before suspension or termination?
No one can say for certain when the situations interrupting transportation through the Suez Canal and Panama Canal will subside, nor what future events will impair other key transportation points. Companies should plan strategies now to reduce the risk of financial loss in the event of persistent or new transportation delays and freight cost increases.